Rocketry
Basic Fin-Stabilized Rockets
These are the first rockets I built, made from scratch using 3D-printed parts, balsawood, and cardboard/cardstock.

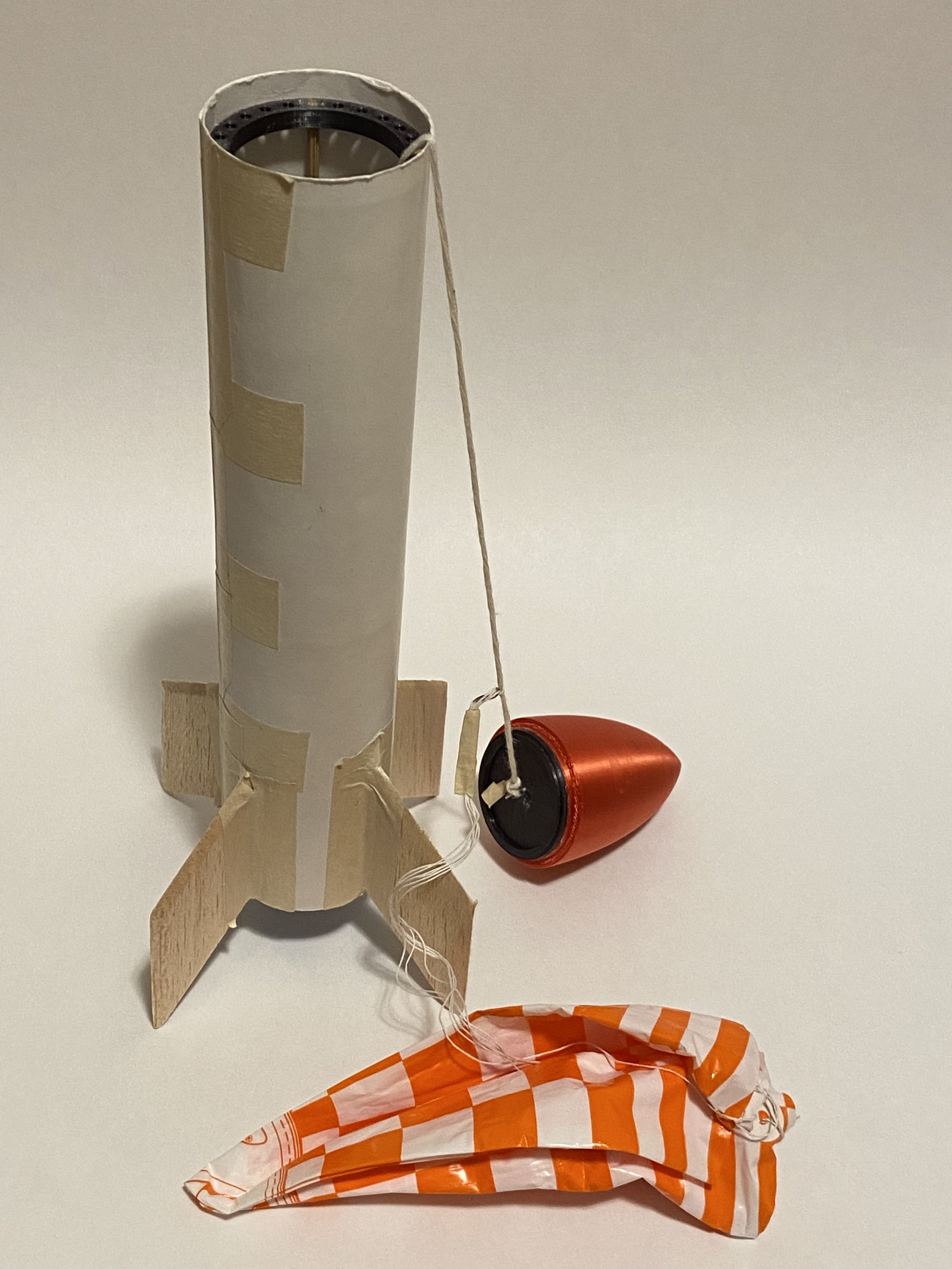
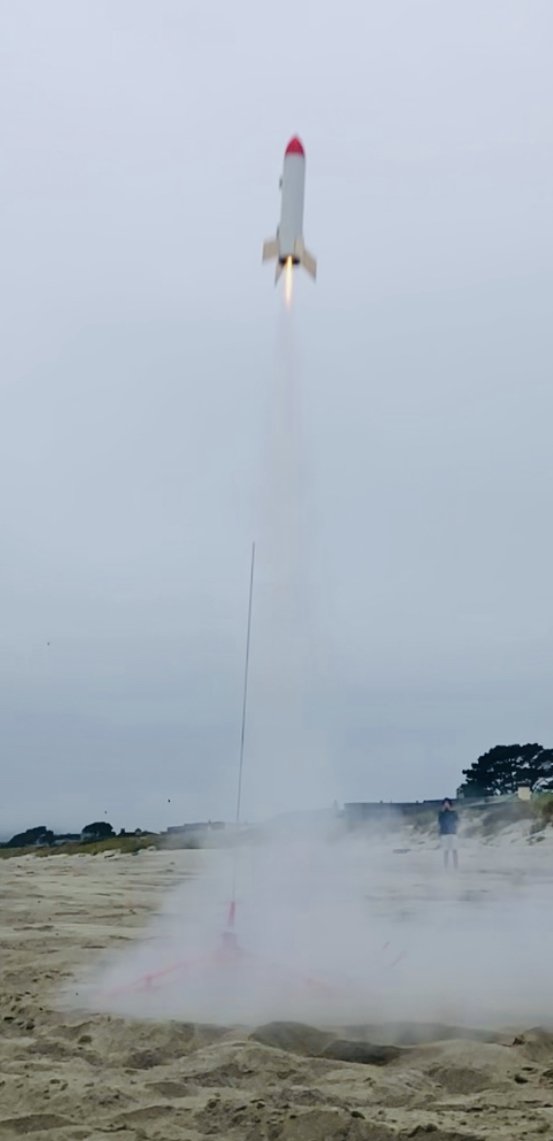
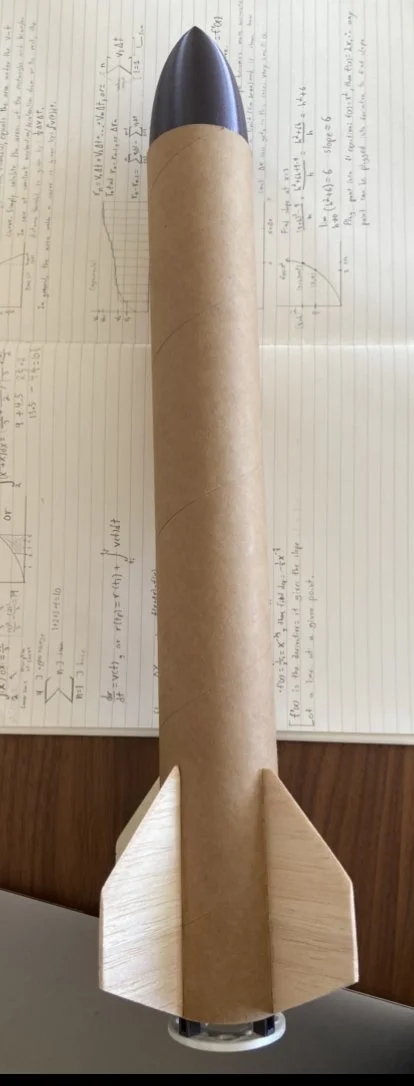
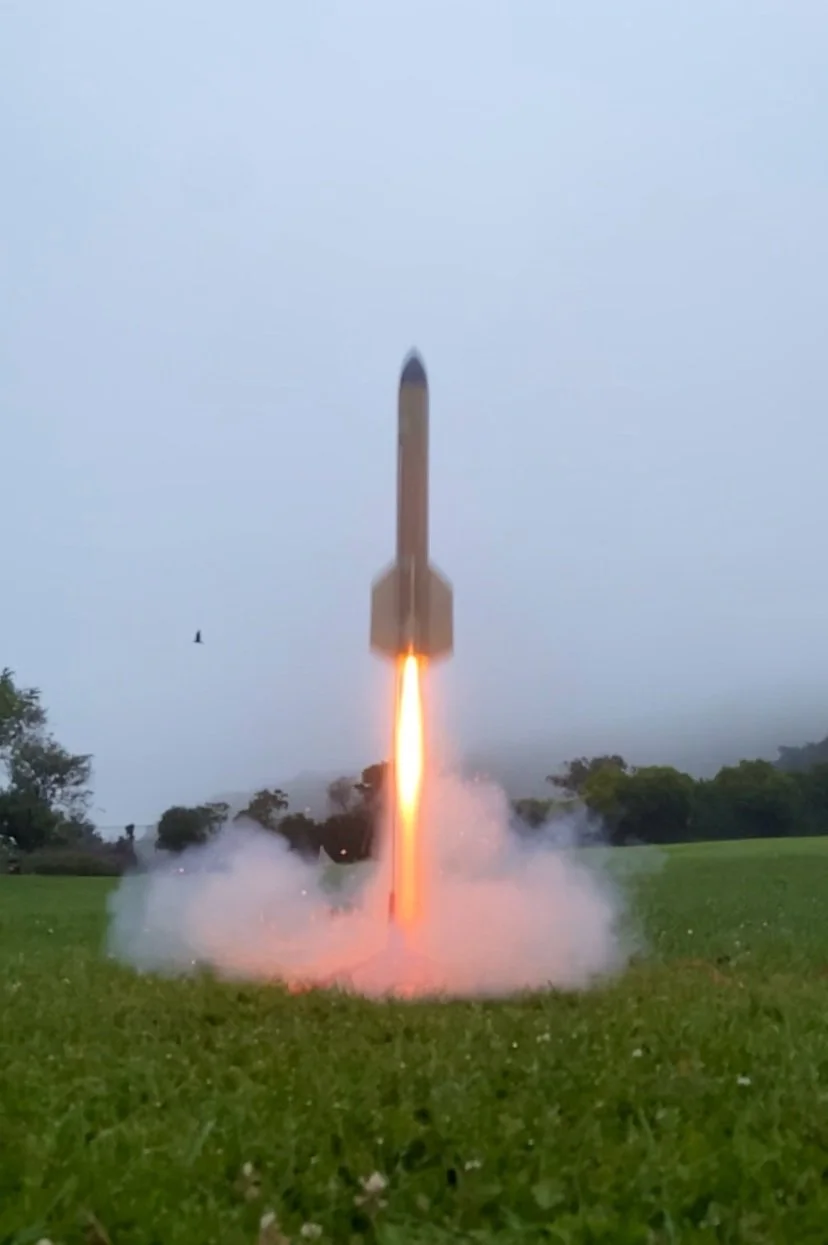
Thrust-Vectoring Rocket
My latest rocket is gimbal-stabilized, and controlled by a custom flight computer. In this flight, you can see the vehicle pitching over and then performing a corrective maneuver using the gimbal. (I use low-powered motors to mitigate the potential risks should the vehicle lose control).

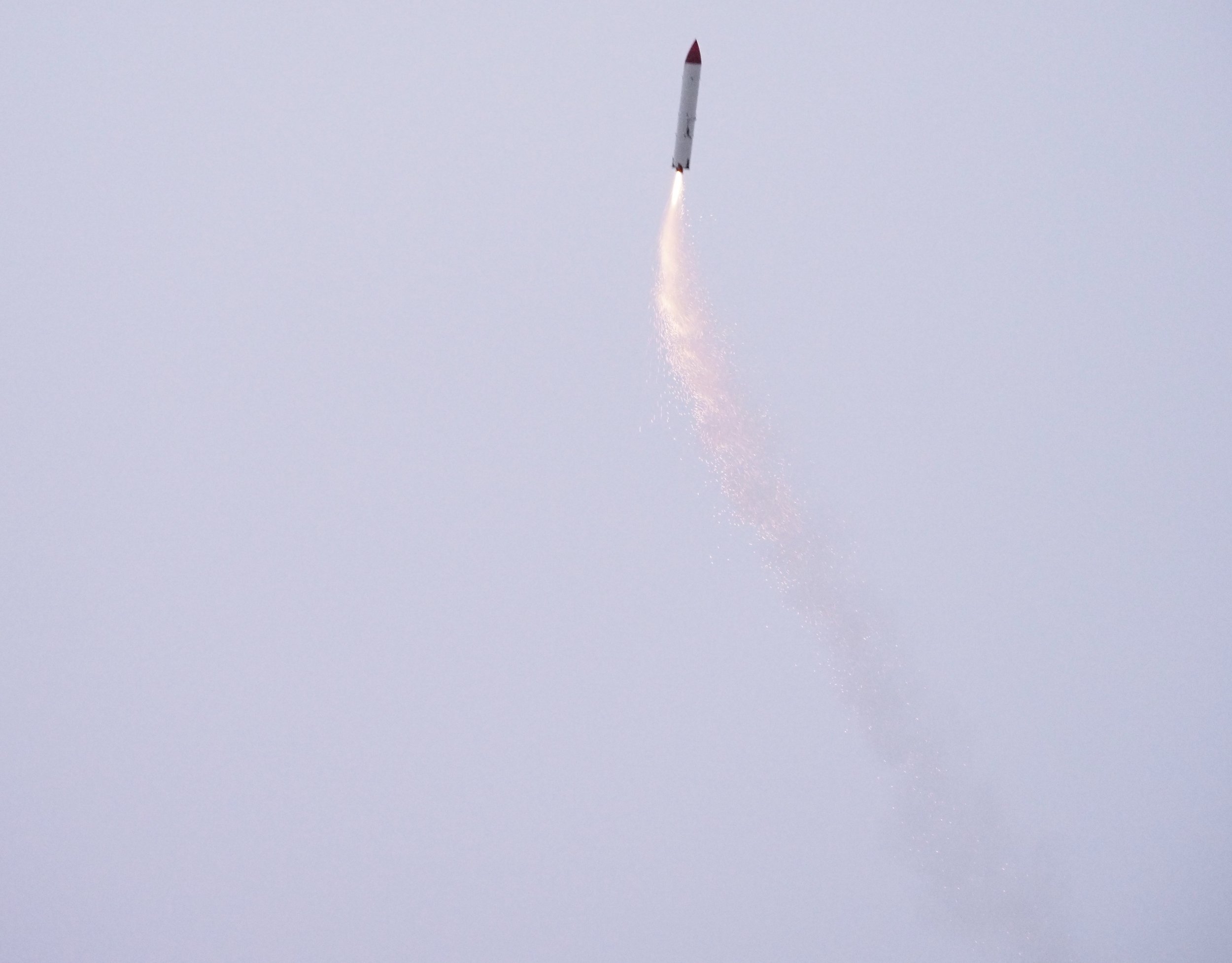

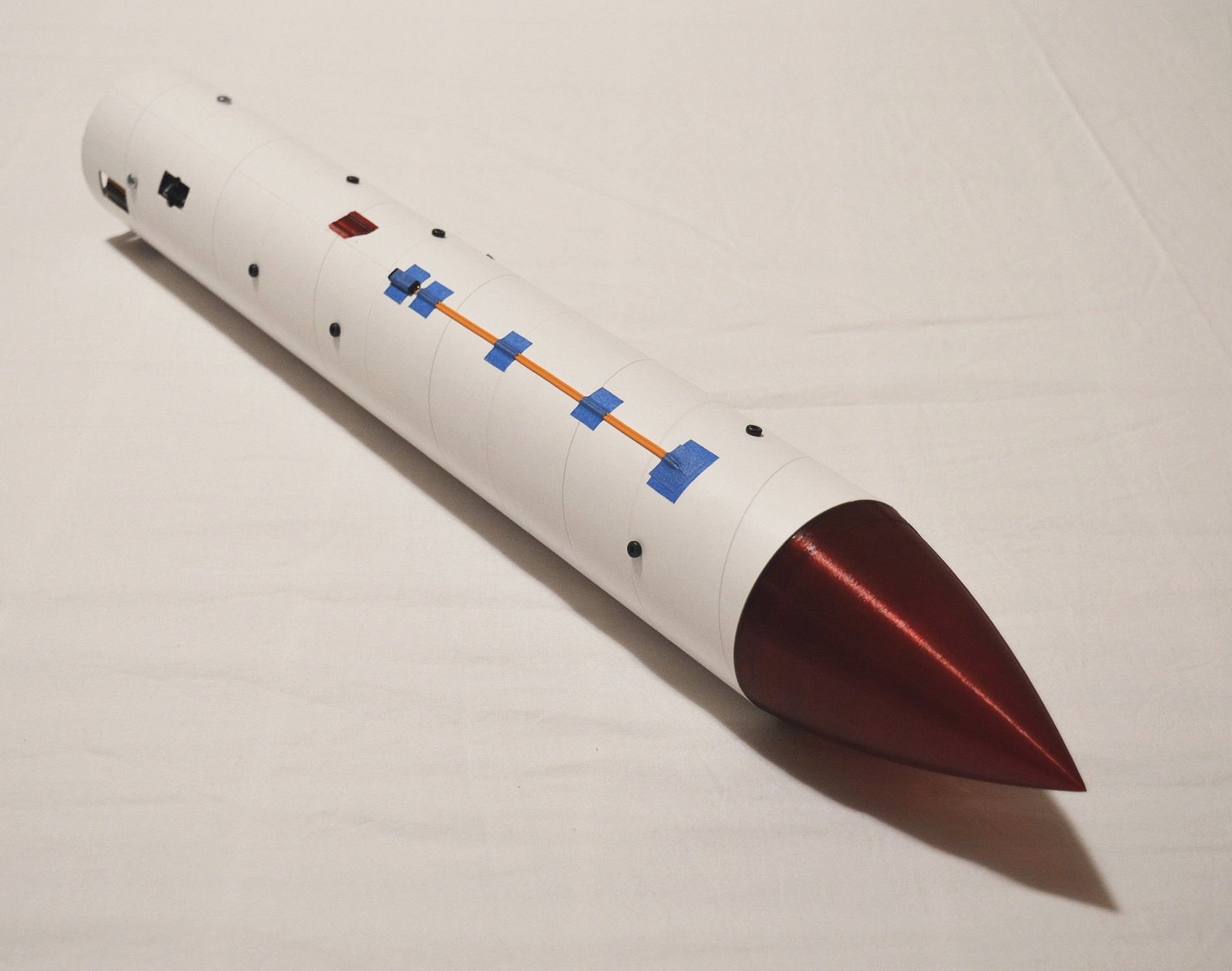
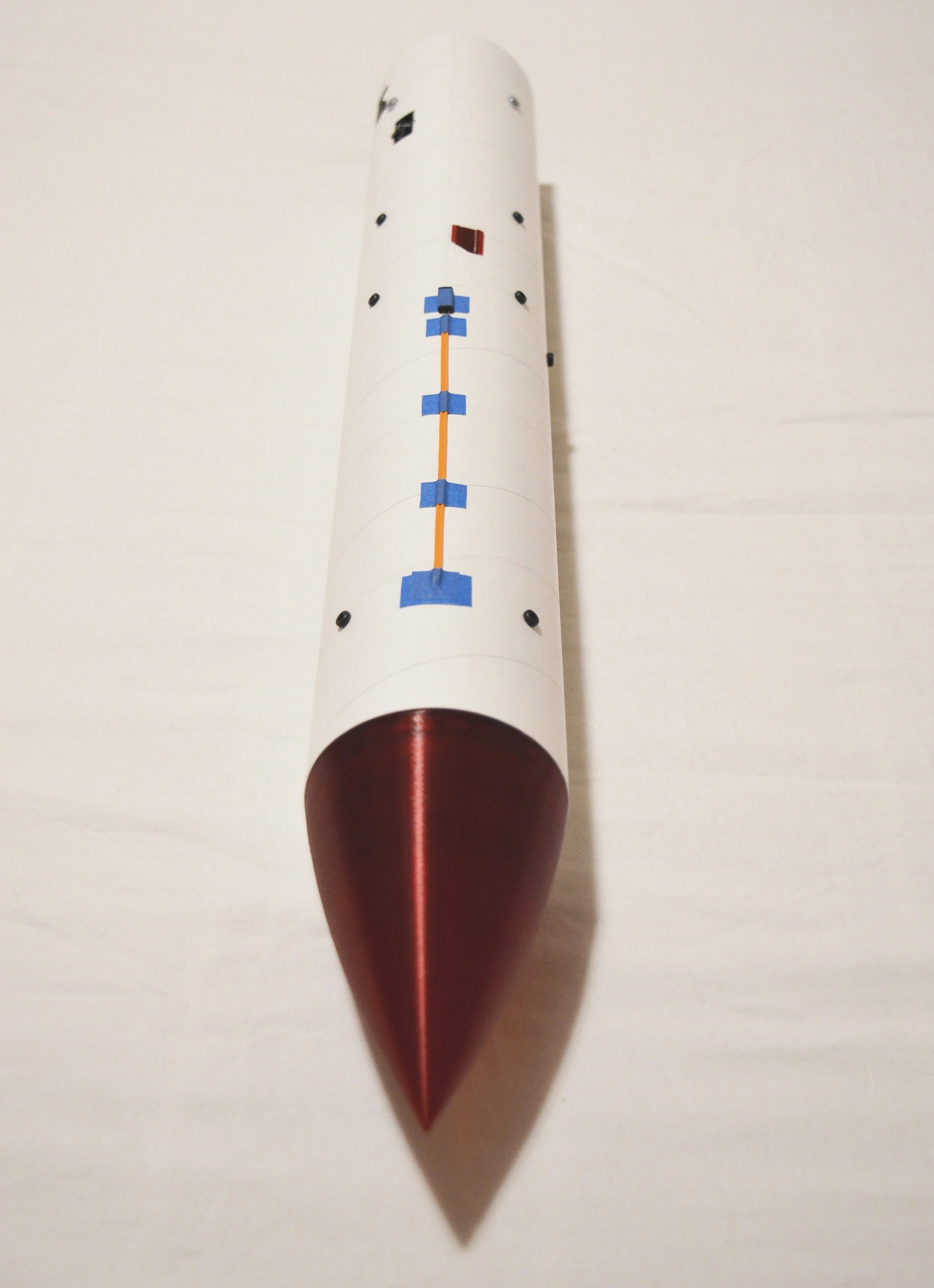
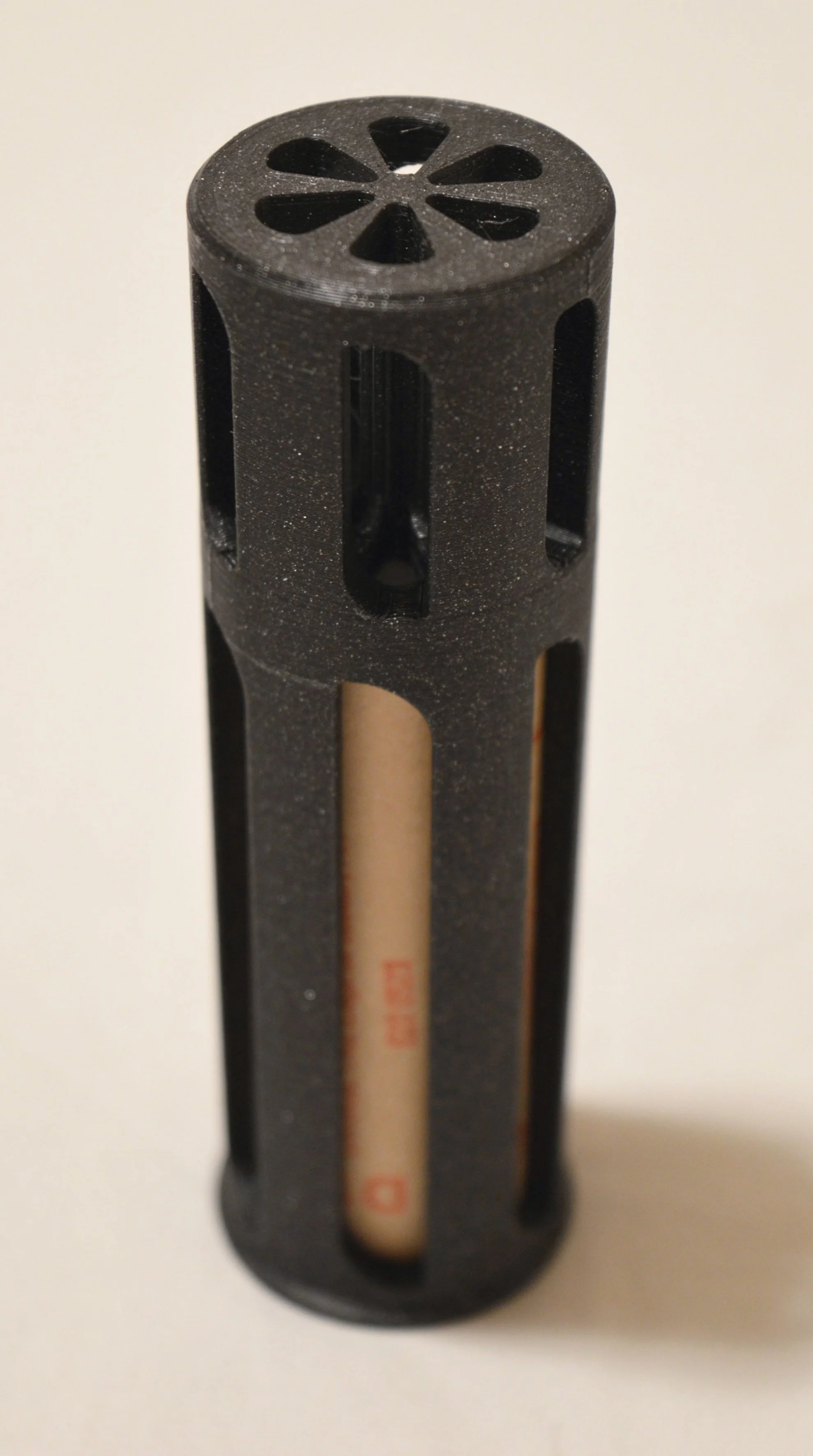
Skeletonized motor adapter

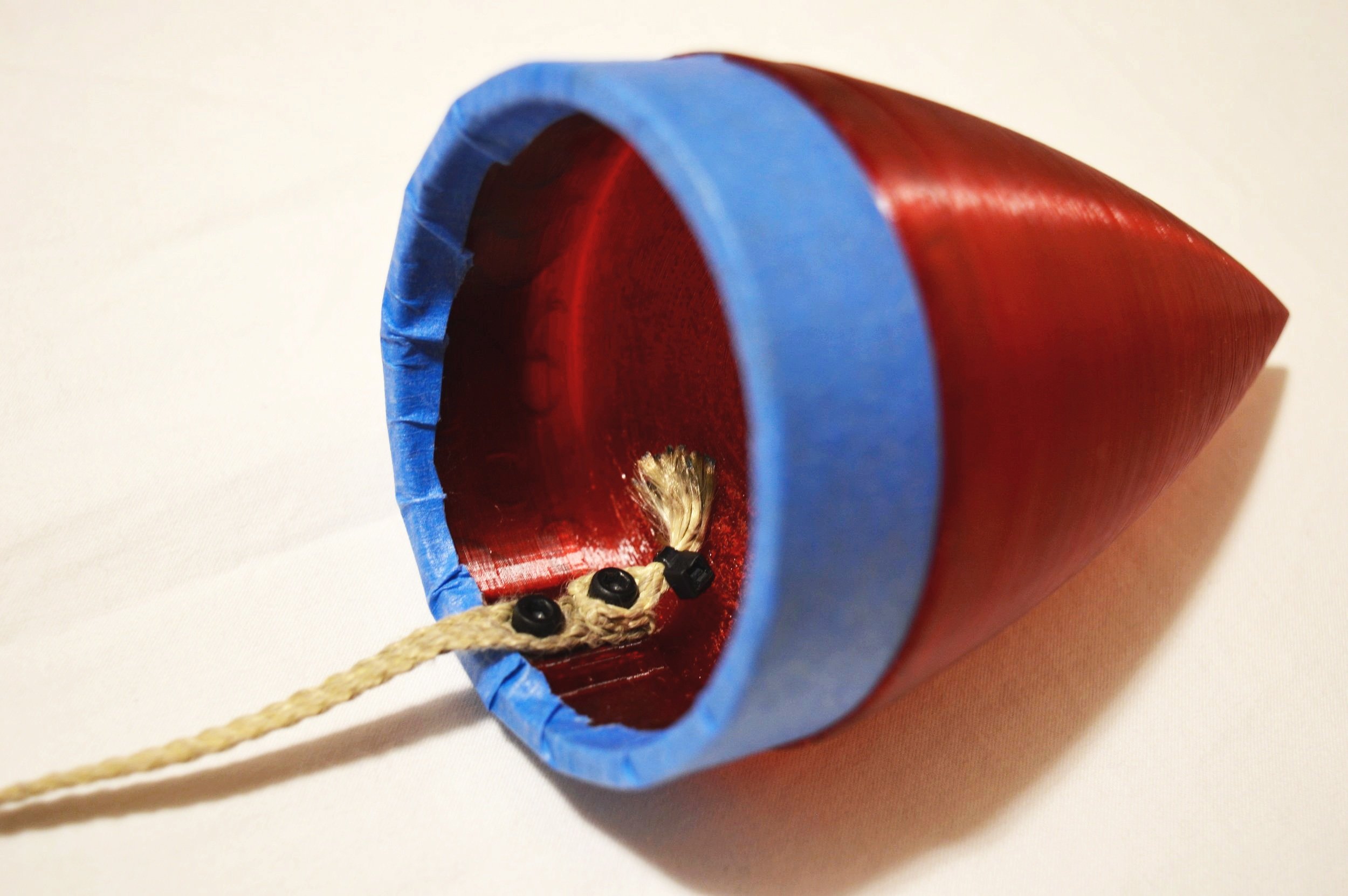
The nosecone features a bulkhead which reduces the effective volume that the gas from the ejection charge needs to pressurize. This reduces the probability of the nosecone failing to separate due to insignificant pressure.

The design of the airframe pressure bulkhead allows for pyrotechnic charges to quickly be replaced between flights, and embedded fastening hardware ensures that corrosive gasses don't degrade the strength of connections over multiple flights.
Launch Footage
Left: Ignition and takeoff (you can see the rocket start to pitch over).
Right: Aerial view of the launch. The rocket corrects its trajectory, but the maneuver is too dramatic and the rocket loses control just as the motor burns out. Just as the rocket is about to touch the ground, the parachute charge ignites and creates a small puff of smoke (The parachute opened too late due to a barometer software error). I later tuned the PID guidance algorithm to be less aggressive to prevent overcorrections.
Gimbal Test
Thrust-Vectoring Rocket: Flight Hardware
Folding Fin Mechanism
Controlled by the rocket’s flight computer, this fin mechanism deploys outward from the airframe during flight. Actuated by a 9V motor, the fins can adjust continuously to control the rocket’s aerodynamic profile (center of pressure). Designed in Rhino, it combines 3D-printed parts with off-the-shelf components like bearings and push-rods.
Version 1
The initial prototype aimed to validate the linkage design, using a central actuator plate driven by a lead screw to deploy or retract six fins.
Version 2
The second prototype improved upon the first by strengthening the central actuator to eliminate play and shortening the linkage arm to reduce actuator plate travel, speeding up fin deployment. Component mass was reduced by 35%, and the lead screw motor was fully integrated into the structure. Additionally, I created a mockup of the airframe section where the fin mechanism will eventually be installed and flown.
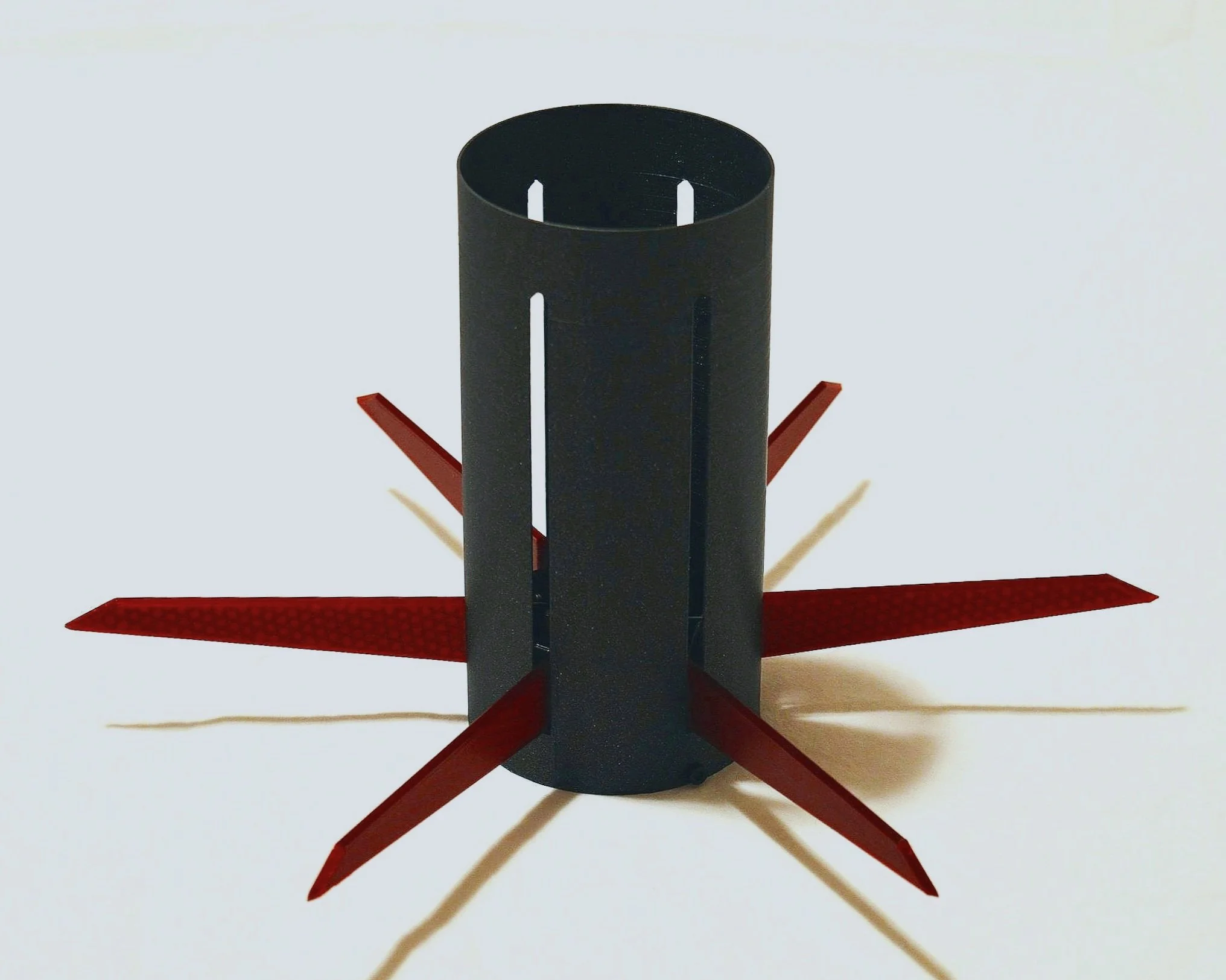
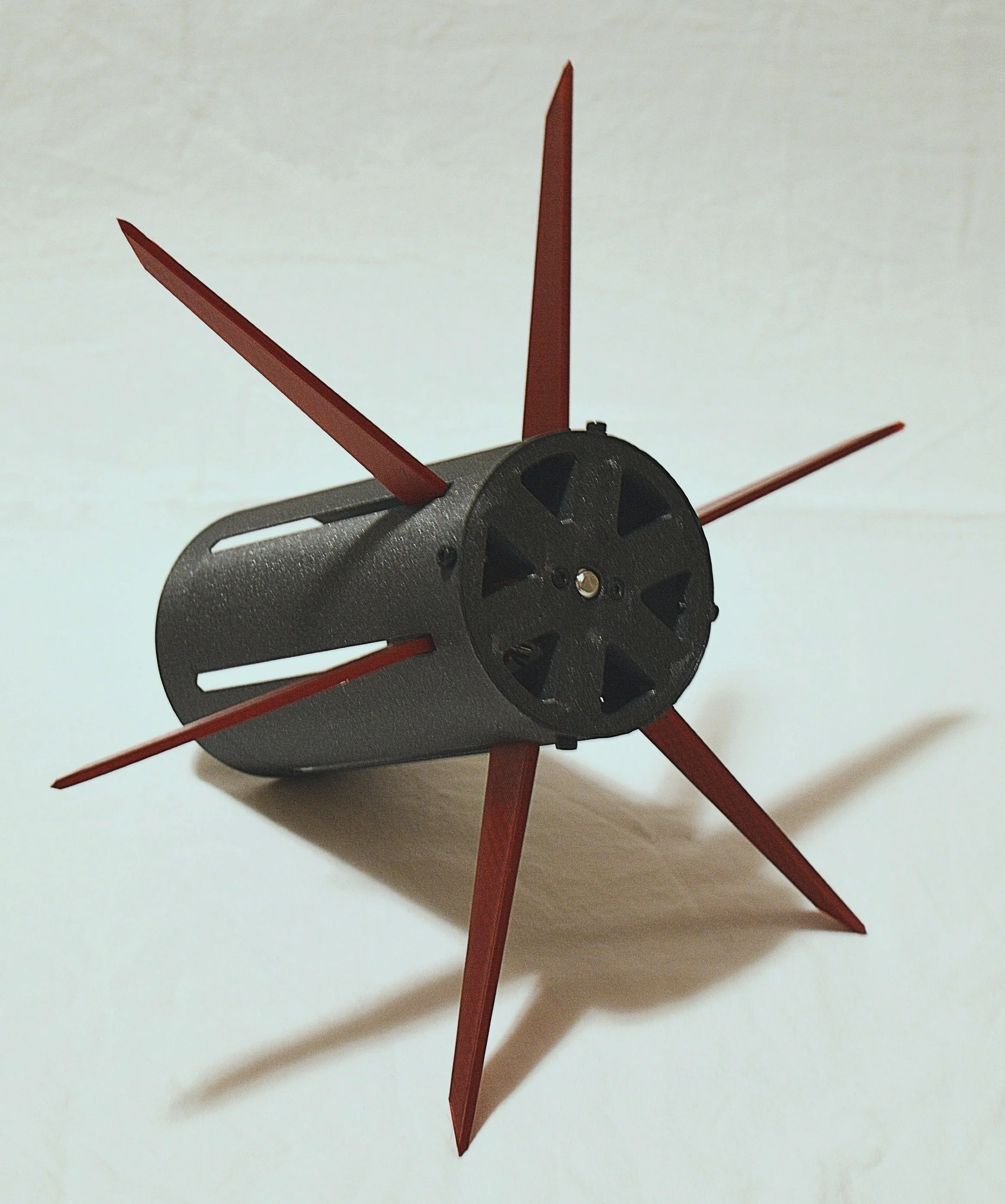


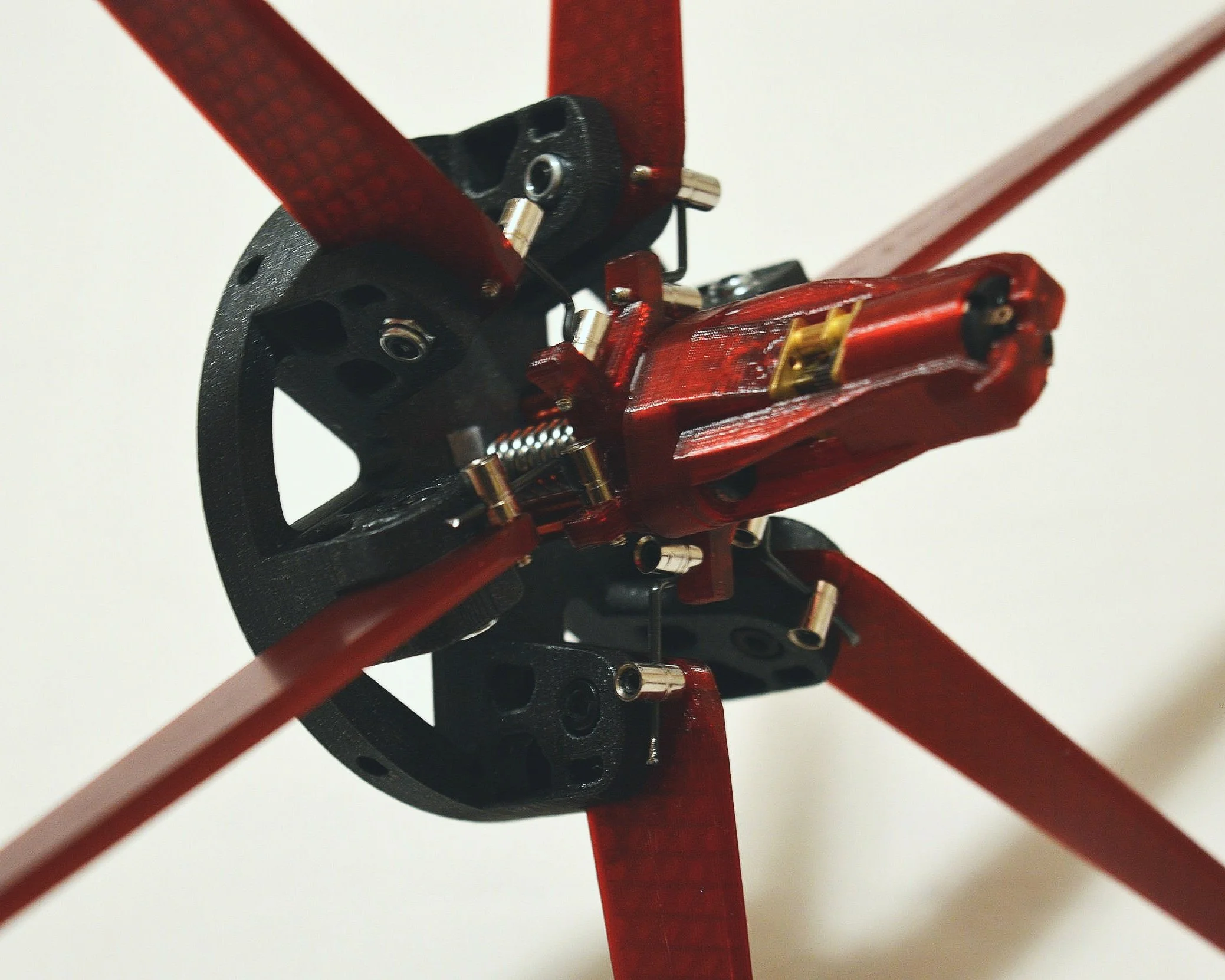
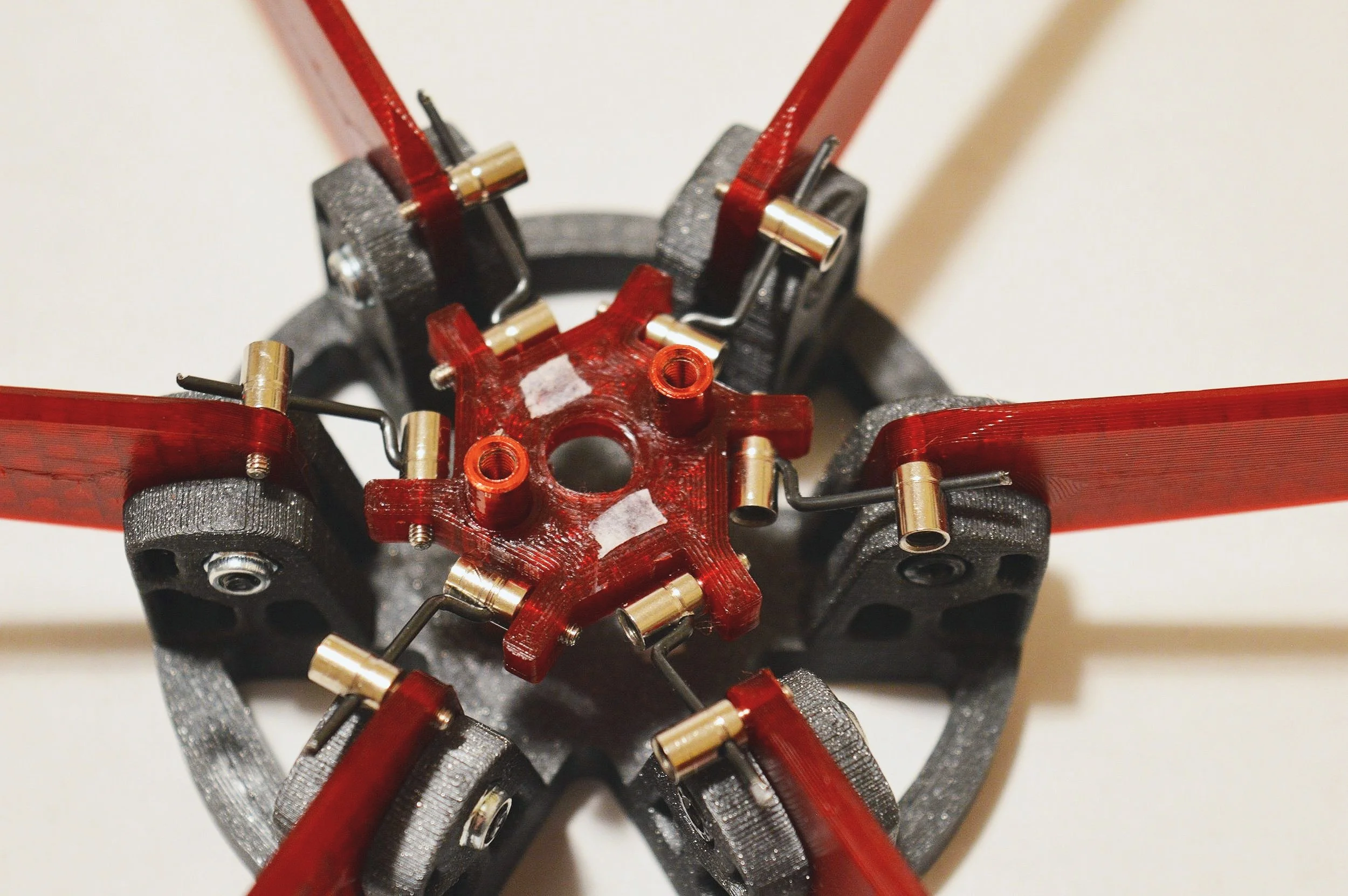
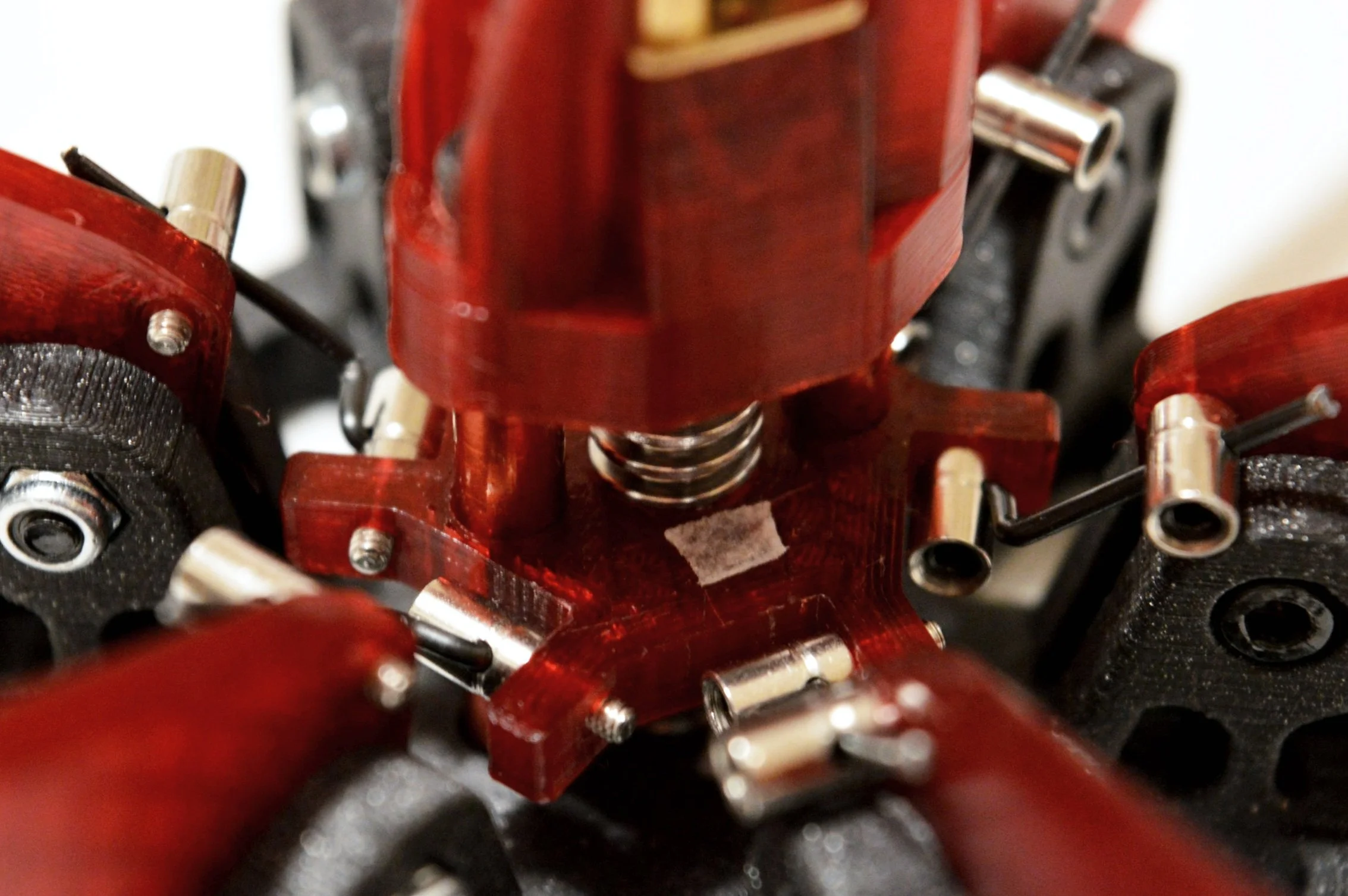
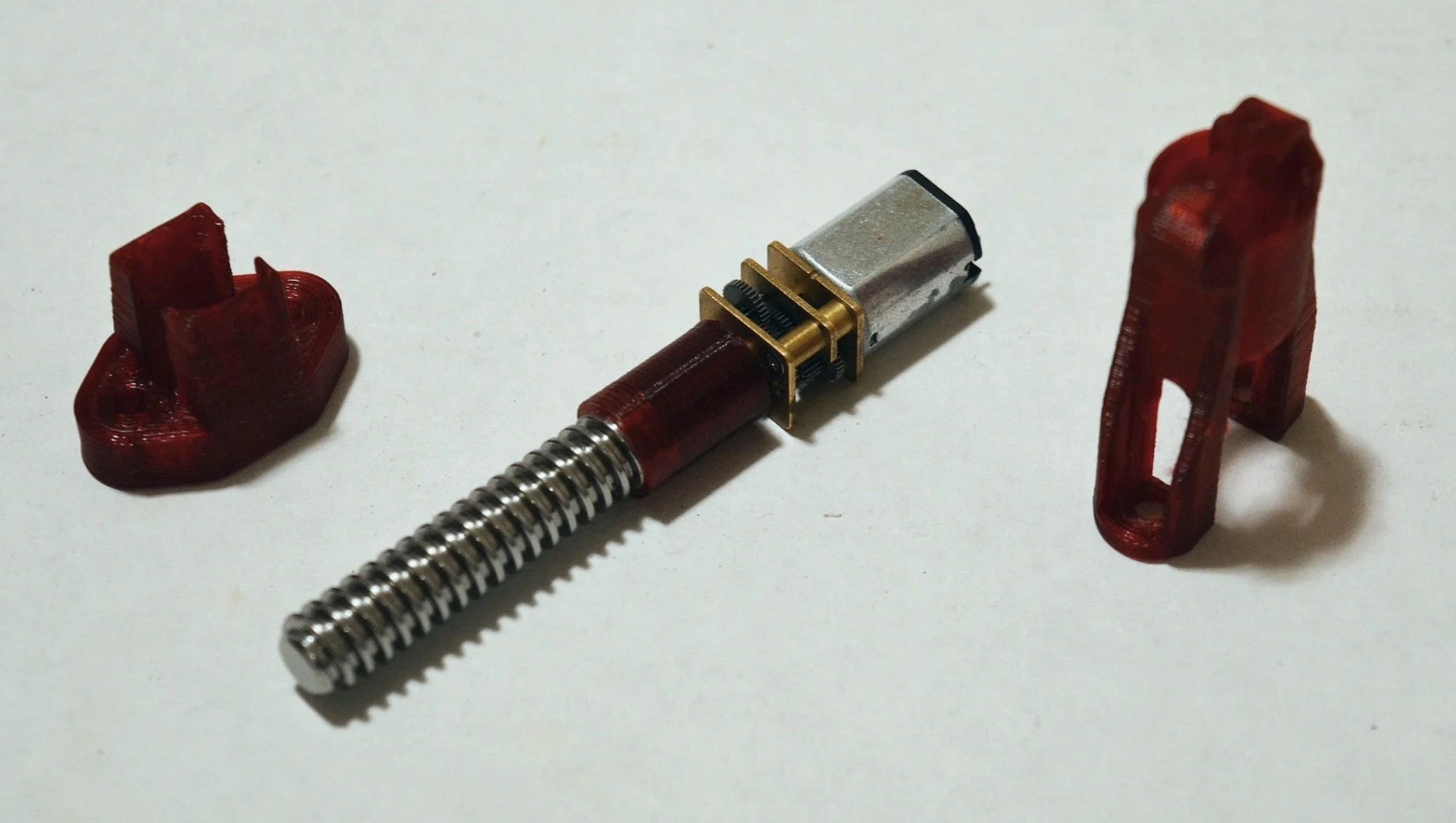
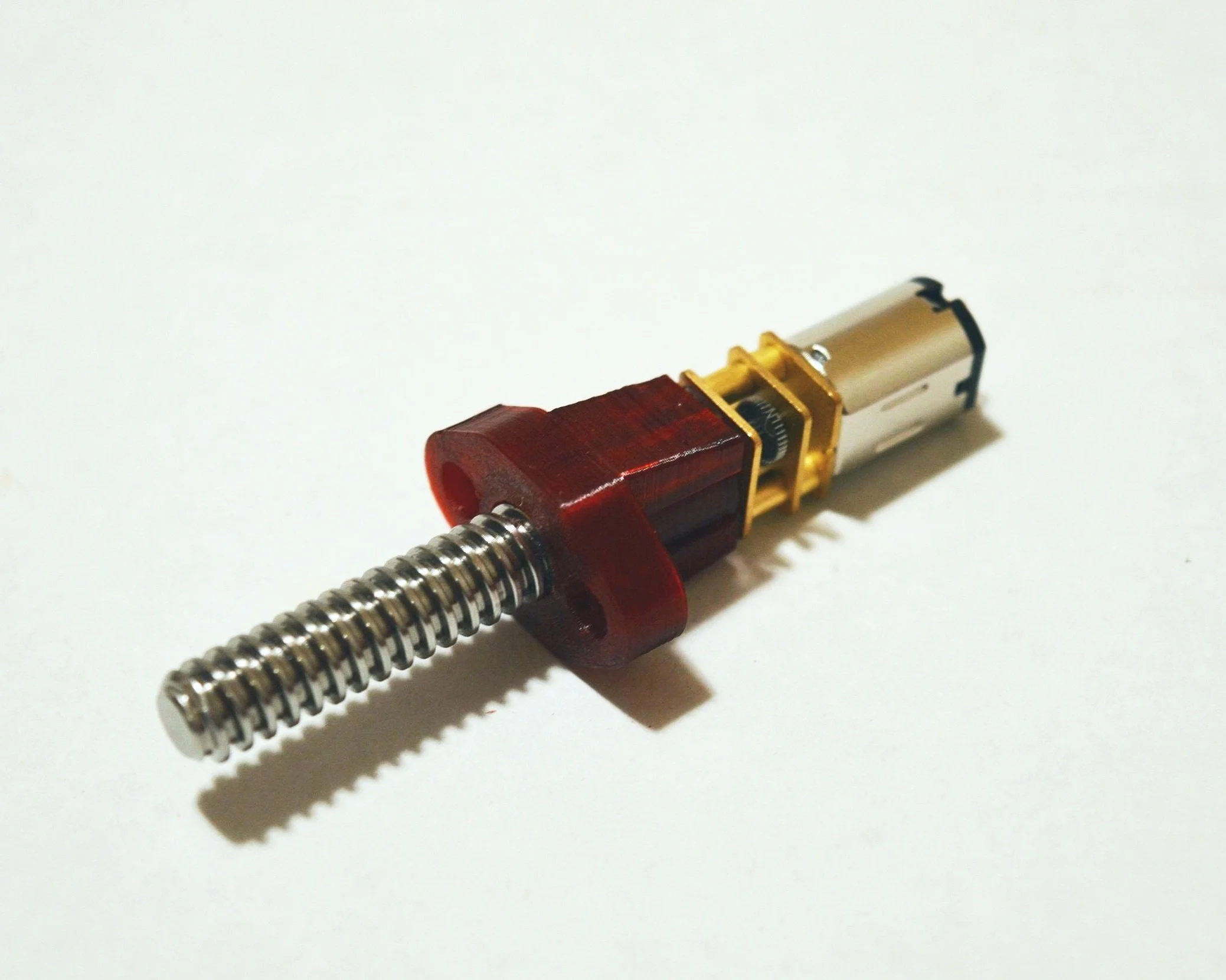


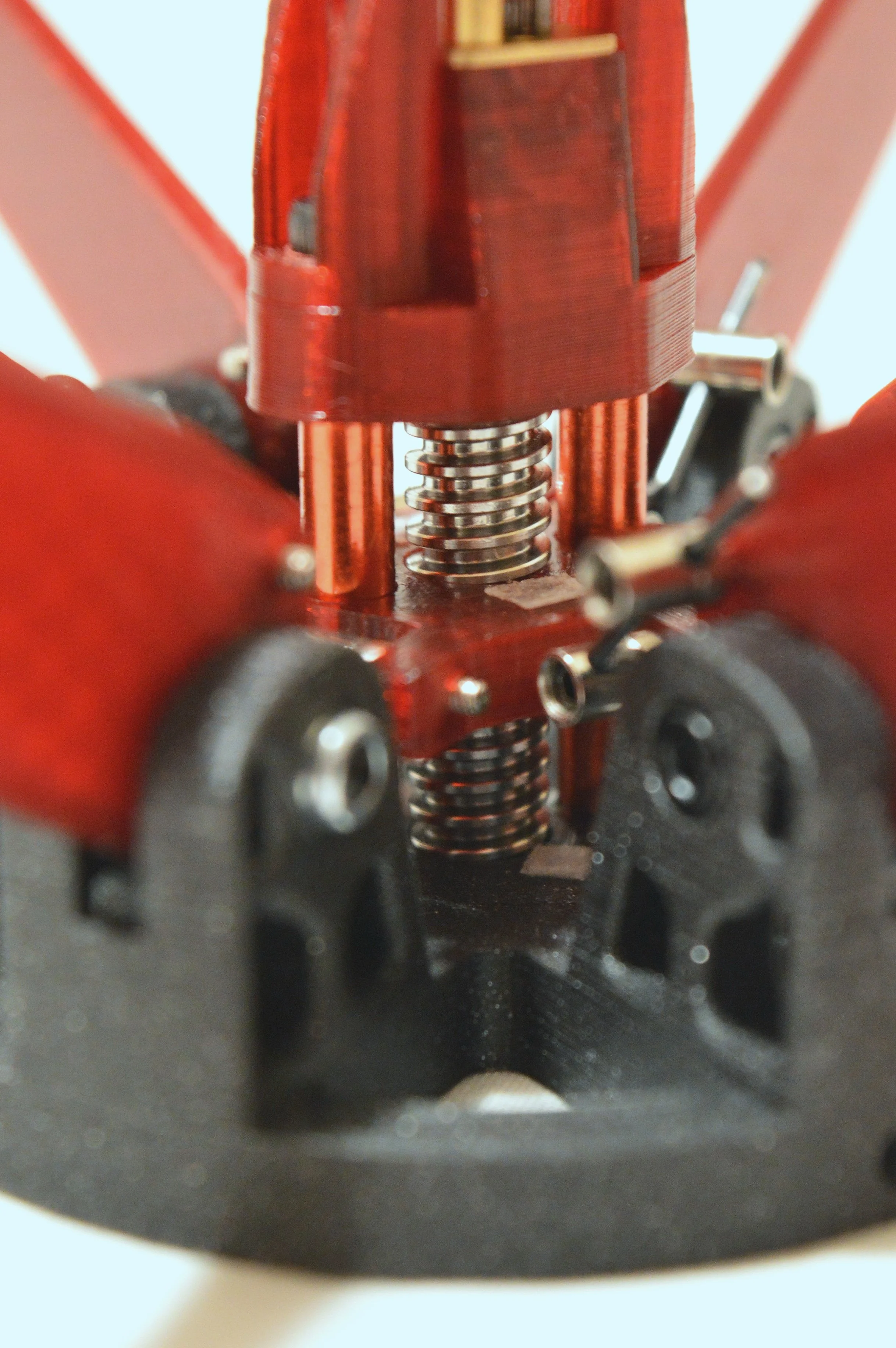
